Consolidation via Modularization
Case: Transferring to modular product structures
The Client:
Heavy Equipment Manufacturer
A global, multi-billion dollar, Swedish company that manufactures mining equipment.
The Challenge:
Implementing Modular Thinking and Practices
The company required assistance to introduce modularization to their product structure. The client had acquired numerous companies and needed to consolidate not only the operations, but also the products and the product structures as a whole. SAM was called in.
The project included 15 sub-projects, where modularization was considered to contribute to a better and simplified product structure, as well as faster development of new end-variants. The sub-projects were both product specific and cross-functional across different product categories. The underlying goal was to support the potential for synergy effects in simplified supply-chain operations and a more coherent product program, i.e. appealing to the customers’ needs.
The Success:
New Design Mind-Set
- Wide understanding of modularization among the designer teams.
- Complete product structures for specific product families at the end of the project.
- The company estimated that their costs were cut with forty-million euro annually
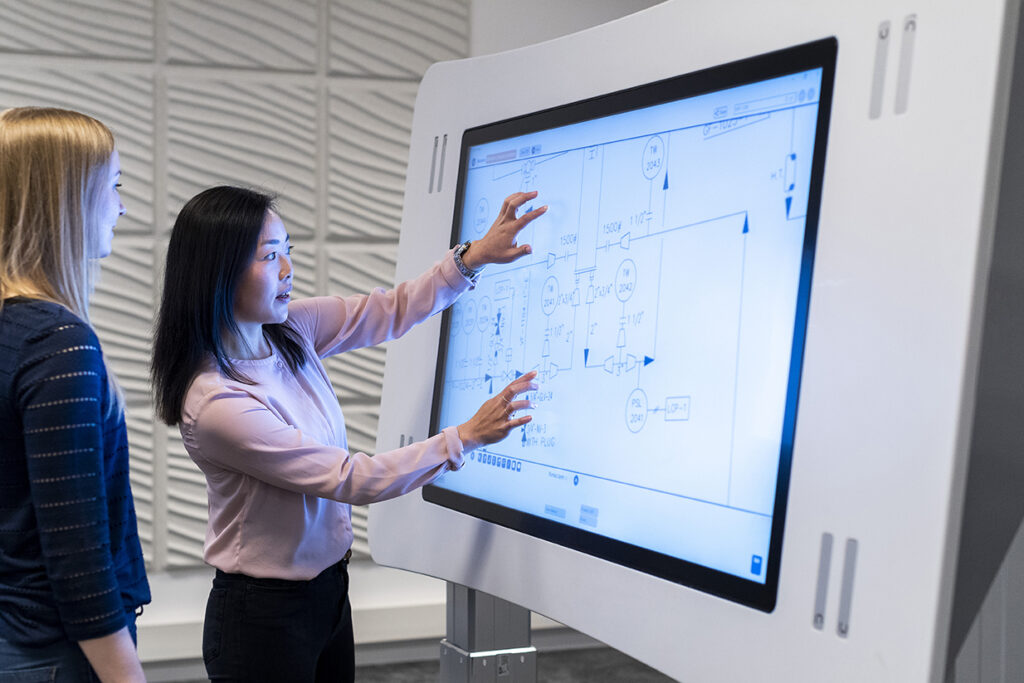
How we did it
The project was a global one and was carried out at several local development departments. Locations ranged from Australia, to several countries in Europe, to both North and South America. Besides training and coaching in modularization theory for both designers and managers, a lot of effort was put on practical applications.
Initially, SAM engaged a substantial group of development managers to define development and design principles. These principles would then grow into a common mind-set and support the alignment of product development over the geographically widespread organization.
SAM contributed with technical definitions, user factors as well as design definitions and relations. In cooperation with the client, SAM also did much of both the data collection and the actual product analysis. Each sub-project was unique and considerable time was spent together with designers on site and out in the field where the equipment was used. All in order to get a deeper understanding of and getting closer to the actual operational factors.
The modular structure made further business possible
One of the design teams received a request for quotation. Unfortunately the design team had focused their time and effort on developing a machine of a different size and performance, not at all matching the requirements.They had, however, worked with a modular strategy and had created a modular product family. As a result, the required structures were defined and ready; instead of the usual 6 months the company needed in the past, it now only took 30 days to reach the requirements in the quotation.
They got the deal and it was the modular structure that made it possible.