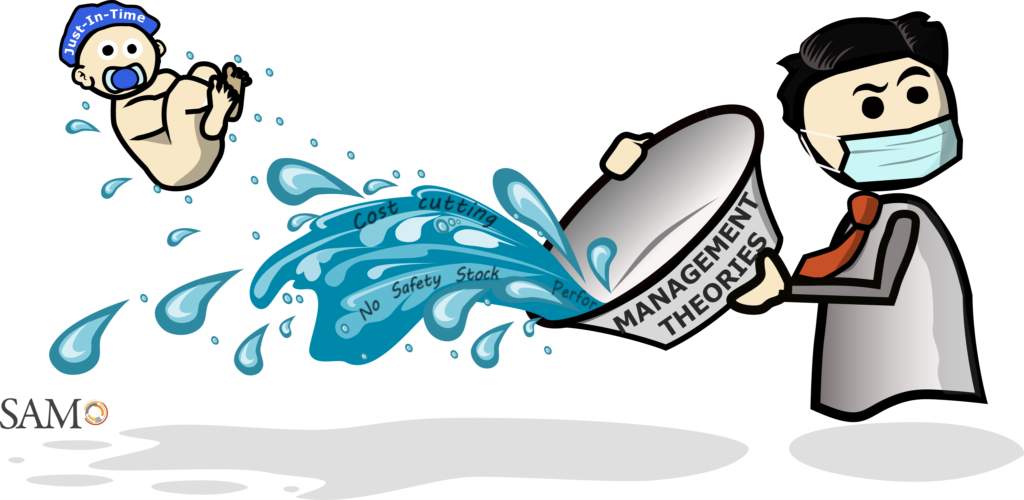
Don't Blame Just-in-time
The ongoing Covid-19 crisis has caught people and organizations across the globe off guard. In numerous places there is a shortage of supply of critical equipment and consumables.
As people start looking for reasons for this situation, several theories are put forward in newspapers, tv-shows and of course on social media. One of the more frequent beliefs is that lean production, and more specifically the principle of Just-in-time has led to a situation where supply chains across all kinds of businesses and organizations are slimmed down to a bare minimum in order to eliminate waste. This is allegedly the reason for the dire situation at hand.
It might very well be true in many cases that an extreme urge to eliminate waste has led to shortages. But is it really the principle of just-in-time that is the culprit?
The concept of just-in-time is not novel in any way, there are examples of this kind of thinking put into practice in various situations dating hundreds of years back. A large-scale systematic approach emerged in the early 1900s and was effectively applied at the T-Ford factory at River Rouge. Later this idea was adapted and refined by Taiichi Ohno, the architect behind the world-renowned Toyota Production System, TPS, that became the model for the management ideal of lean production.
The central idea of just-in-time is to produce what is needed when it is needed in the amount and quality needed – nothing more, nothing less. By doing so throughout a value chain, where each actor thinks and acts this way, highly efficient flows can be achieved with very little waste. This is what the critics of this idea believe is wrong. They argue that just-in-time leads to minimized buffers and no safety stock – and that is why we today see disastrous shortages of life-saving equipment.
However, the principle of just-in-time doesn’t rule out keeping safety stocks of critical items. On the contrary, just-in-time brings control over the amount of supply throughout the flow. Instead of having stocks of fluctuating sizes as a result of arbitrary plans and decisions, the well-defined buffers employed in just-in-time-flows allow for precise control and conscious decisions on how much to keep in each buffer. This also means that you can make conscious, well-informed decisions about safety stock of critical items (such as protective gear and medicines).
One fundamental aspect of just-in-time, that the critics seem to miss completely, is the fact that it uncovers imperfections, flaws and deviations in any system. As such it becomes the driving force behind continuous improvements. In this capacity, just-in-time has been one of the most important factors behind the rapid global increase of wealth and quality of life over the past century. Persistent and mindful application of just-in-time has made companies and organizations significantly better at handling all kinds of crises. It is no exaggeration to say that just-in-time has improved quality of life for billions of people all over the world.
As with any idea or concept, if misunderstood and applied wrong, the results will not be the desired ones. That does not mean that the idea itself is wrong.
Just-in-time applied in the right way has literally saved lives in the past, it saves lives now and it will save lives in the future – it would be a tragedy for humankind to abandon this idea!