Planning of Durability Testing
Case: Visual planning methods for bottle-neck testing operations
The Client:
Global Truck Manufacturer
The R&D department at a truck manufacturer. The department had 1,000 employees and the company produced 70,000 trucks annually.
The Challenge:
Bottle-necks in Test Equipment Availability
SAM was assigned to improve the flow from the R&D department and SAM sensed that one of the design teams was under a lot of stress. They had problems meeting deadlines due to project overload and too many checklists to follow. The expectations on the group were high, as the team was responsible for meeting the increasingly extensive legal requirements.
The Success:
No Need for New Test Equipment
- Increased productivity in the design department, thus bringing major competitive advantage compared to the competitors when adapting to new legal requirements.
- Improved utilization of the test cells.
- Each test carrier got the needed attention in order to start on time.
- Tacted production during testing.
- A common view of the whole design organization.
- The organization went from working in individual silos to having a common aim and holistic mind-set.
- A sense of calm and control in the design work.
An additional benefit was that the results from the project were spread to and adapted by the rest of the R&D department.
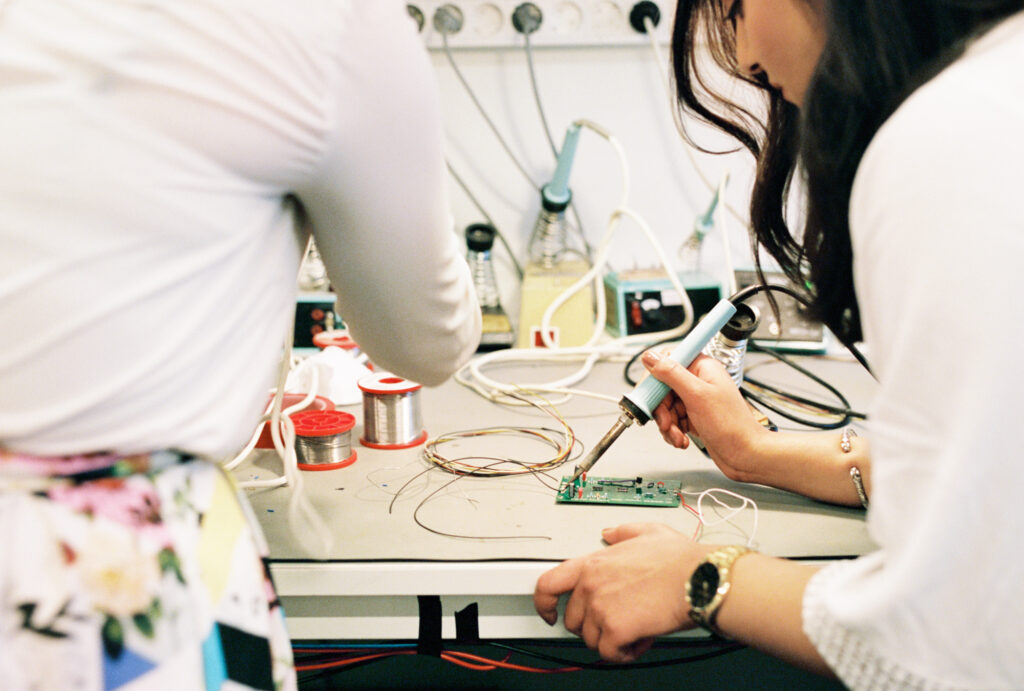
How we did it
SAM supported the design team in understanding the true needs in their product development operation. It turned out that the team was working towards project goals that were more or less fictitious. By interviewing the employees and reflecting upon demand driven flow, the group realized that the real need was to have the developed parts on site by the time that the mandatory durability test that each part needed to pass took place.
Further, SAM and the design team realized that the planning of the durability tests was inadequate. The current goal was to guarantee full utilization of the test cells, leading to over-scheduled production. Yet, the planning of the test cells was uneven and parts were missing for tests, as the different design teams were not working towards the same test deadlines.
The flow was evened out by creating a visual planning board, where a new test carrier went into the test cells with a tact time of two weeks. The test carrier was symbolized by a card that was moved forward on a whiteboard, towards the test cells, every other week.