Merging product programs
Case: Using modular design to merge two product programs and organizations
The Client:
Construction Equipment Manufacturer
One of the largest divisions of a Fortune 100 multinational construction equipment manufacturer. The R&D departments were situated in Germany and Japan with nearly a thousand employees.
The Challenge:
Worlds Apart
The two product programs historically came from two acquired companies on opposite sides of the world with large cultural- and language differences. Since the products are similar, but not identical, in functionality, the potential for sharing components (and all the processes and operations around e.g. development, testing, suppliers, production etc.) were large.
While technically challenging, the largest challenges were difficulties relating to communication, strategy and goal alignment, common understanding, change of habits and processes, project management, interpretation of customer need and requirements since, in order to merge the physical products, first, the thinking, methodology and softer aspects of the two organizations had to be merged.
The Success:
Common Ground
- Common understanding of modularization throughout the organization
- Agreement and alignment on how to assess design through both customer need, operational factors and cost evaluation.
- Sharing of main components, suppliers, processes and documentation
- Fewer (up to 50%) parts, with maintained product variation.
- Similar product architecture
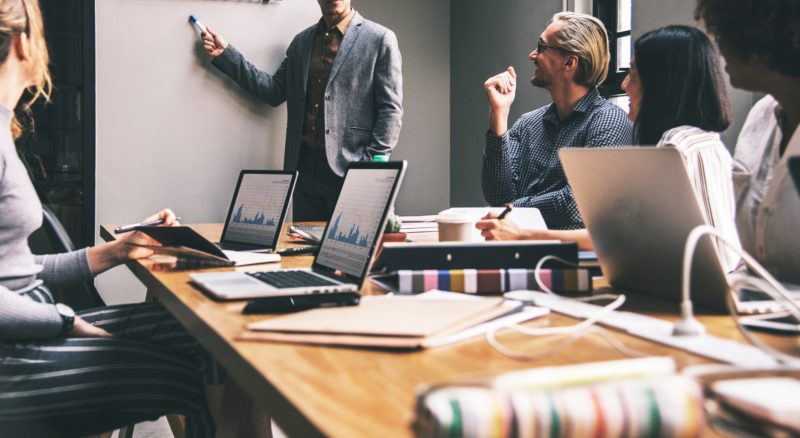
How we did it
Apart from participation in the daily work and on the job training in concept design, a vital part of creating common ground is for the whole organization to understand modularization in depth. Different means and approaches such as training programme, guidebook material, field- and study visits, workshops etc. were used to reach out to the whole organization to create the back bone for alignment in thinking and working. The merged product program would come as a consequence of this.
Working as the mediator and link between the two different organizations, we focused on achieving common ground by agreeing around modular principles, ways and means of working, rather than taking sides for particular technical solutions.
Since the cultural-, organizational-, process- and technical changes does not (and should not) happen over night, we focused on particular subsystems and components as practice grounds to create good examples, inspiration and success stories to build the competence and tools required for the organization to gradually spread it to other parts.