Improving process line efficiency
Case: Improving the yield and reducing waste in food production
The Client:
A Century of Production
A large, French food production company founded in the late 19th century. Over the years, the company has spread throughout Europe and has a yearly turnover of 200 MEUR.
The Challenge:
An Under-Producing Line
In one of their factories the company had invested in a new production line. The investment was a necessity to achieve growth in new product segments and attract new customers. Unfortunately the efficiency of the line was poor, limiting the yield. Even several years its installation, the line didn’t live up to the production expectations.
Radical changes to the line had to be made, and soon, or the owners would close the unprofitable line. Production efficiency had to improve and SAM was involved to increase the yield of the line.
The Success:
Increased Line Efficiency and Operator Satisfaction
- 30% increase in productivity within 6 months, reducing the waste in half. The line was now profitable.
- A change of mind-set, striving for cooperation and learning.
- A change of culture at the factory, pertaining both management’s and operators’ behavior.
- A better and more appreciated workplace with less stress.
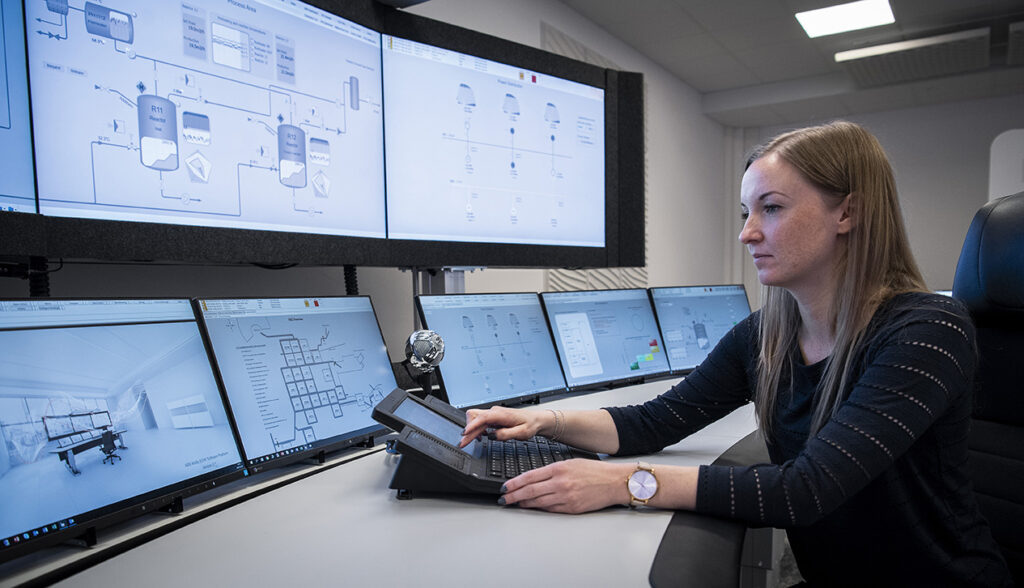
How we did it
SAM’s first challenge was to bring back the production line to a normal situation; people needed to be able to breathe again, they needed to recover their strength and work motivation. Additionally, standards had to be set, documented and followed. To accomplish this SAM worked in close contact with the people at the production line, documenting their best-practices and other habits to use as a base for improvement. SAM also promoted more cooperation between the production line operators and other departments, i.e. maintenance.
By asking the right questions and by following up with key issues, a learning culture started to flourish. This new culture and behavior was soon reflected in the efficiency of the line.
Meanwhile, SAM realized that the company would need additional support to make the improvements sustainable and to ensure long-term benefits. The key was to strengthen the site’s culture through its managers. The company’s strategy already emphasized that people were core of their systems, which is also the central pillar of SAM’s Management by Means (MBM) framework. Therefore, MBM coaching was conducted to form and align the culture at the production site with the culture and principles of the company as a whole. Nowadays people are more keen to collaborate – cooperating to make beneficial improvements for the company. As a bonus, they are also more confident to challenge the system, striving to make the company long-term sustainable.