Just-in-Time Maintenance
Case: Efficiency improvements of maintenance
The Client:
Steel Producer
A major Swedish producer of specialized high-strength steel.
The Challenge:
Low Maintenance Capacity
The company had issues sustaining adequate capacity in maintenance at the steel manufacturing plant to enable continuous casting. The steel plant had been pushed to maximum capacity due to an increased quote of high-strength steel variants in the production and demanded much maintenance. The common perception was that the plant was under-staffed, needed more space for maintenance and was too out of date to function properly.
The Success:
Shortened Lead-Time for Maintenance
- The main goal of managing the increased need of maintenance was obtained quickly, and without any further investments.
- Other departments were able to utilize more space, thanks to the reduced need of space in the maintenance plant.
- Lead times were generally shortened and the tied up capital was reduced.
- Waste in terms of over-production was eliminated.
- The largest gain was perhaps the employee satisfaction. Employees were given more power and opportunities to influence their work situation, in addition to a clear sense of how their work affected the whole production flow.
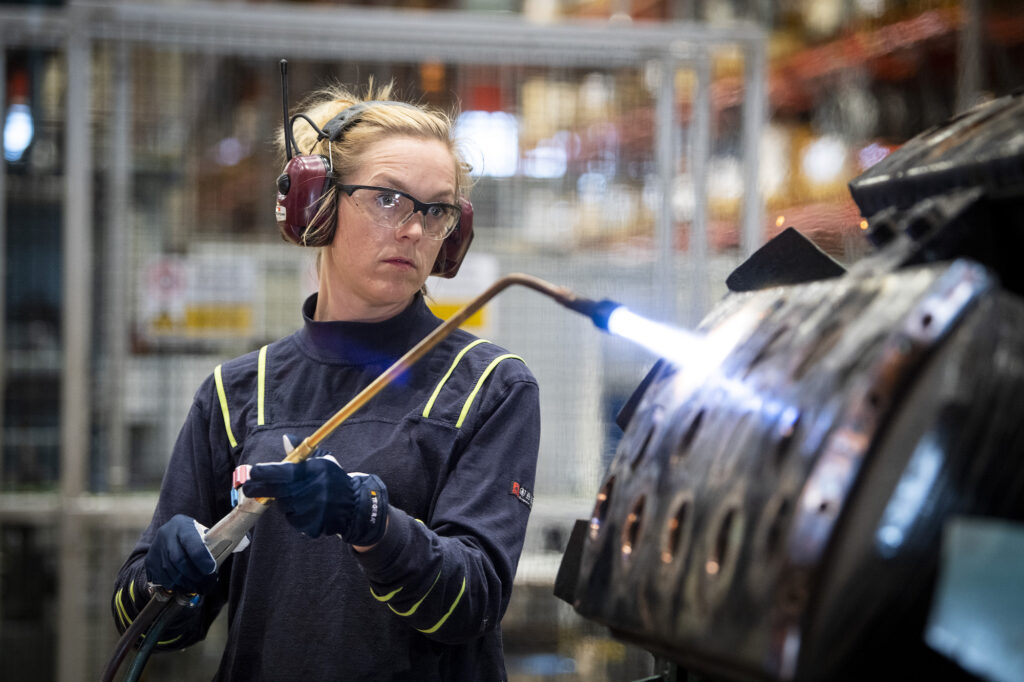
How we did it
SAM got involved in order to find an alternative solution. By carefully studying the operation and gaining a detailed understanding of the issues, a tailor-made training program was developed. The program involved employees and leaders within the whole maintenance flow. The aim was to support the employees with new principles and methods, training the staff in their daily operations.
The introduction of a consumption driven flow, with pull-buffers built on just-in-time theory, was key. In parallel, SAM worked with management and employees in order to establish a continuous improvement structure, according to the principles of MBM. All co-workers were involved to safeguard that the new way of working would continue to last long-term.